Lean manufacturing adalah suatu metode produksi yang bertujuan untuk menghilangkan pemborosan (waste) dalam proses produksi sehingga dapat meningkatkan efisiensi dan produktivitas secara keseluruhan.
Metode ini menjadi populer dari Toyota Production System yang dikembangkan oleh Taiichi Ohno pada tahun 1950-an. Penerapan lean manufacturing tidak hanya berlaku di industri manufaktur, tetapi juga dapat diterapkan di berbagai bidang, termasuk layanan dan administrasi.
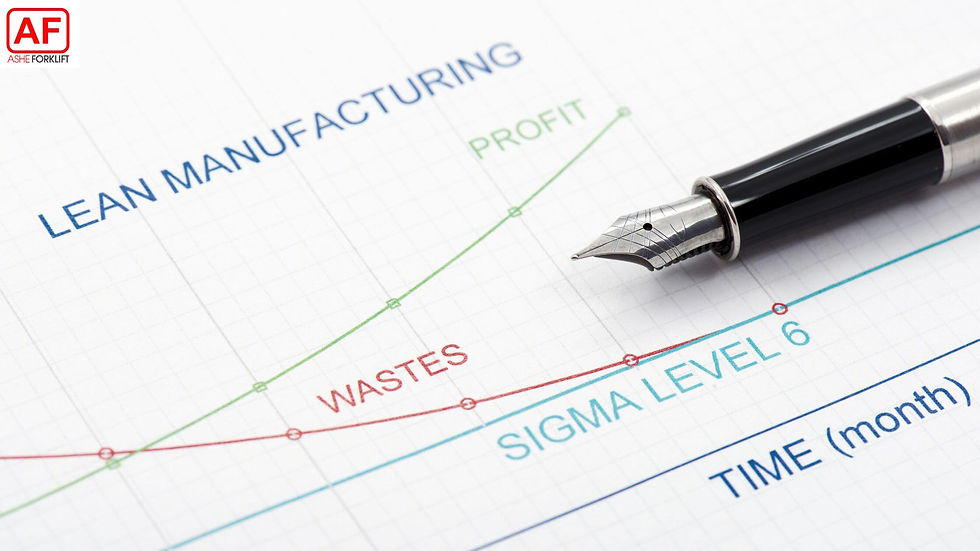
Lean manufacturing adalah proses produksi berdasarkan ideologi memaksimalkan produktivitas sekaligus meminimalkan pemborosan dalam operasi manufaktur. Prinsip lean melihat pemborosan sebagai segala sesuatu yang tidak menambah nilai yang bersedia dibayar oleh pelanggan.
Juga dikenal sebagai produksi ramping, metodologi ini didasarkan pada prinsip-prinsip manufaktur khusus yang telah memengaruhi sistem produksi di seluruh dunia serta industri lainnya termasuk layanan kesehatan, perangkat lunak, dan berbagai industri jasa.
Key Takeaways
Lean manufacturing adalah suatu metode produksi yang bertujuan untuk meningkatkan efisiensi produktivitas.
Lean manufacturing memiliki sejarah yang panjang, serta telah diterapkan di banyak perusahaan raksasa di seluruh dunia.
Penerapan prinsip-prinsip lean manufacturing dapat memberikan beberapa keuntungan dan kekurangan, tergantung pada bagaimana dan pada apa diterapkan.
Prinsip-prinsip Lean Manufacturing
1. Value (Nilai)
Prinsip pertama dari lean manufacturing adalah memahami nilai dari produk dari perspektif pelanggan. Dalam hal ini, nilai adalah segala sesuatu yang dianggap penting oleh pelanggan dan mereka bersedia membayar untuk itu. Oleh karena itu, perusahaan harus memahami kebutuhan dan keinginan pelanggan serta memastikan bahwa produk yang dihasilkan dapat memenuhi kebutuhan tersebut.
2. Value Stream (Nilai Aliran)
Prinsip kedua adalah memahami value stream atau aliran nilai. Aliran nilai adalah serangkaian proses yang diperlukan untuk menghasilkan produk yang memiliki nilai bagi pelanggan.
Prinsip ini bertujuan untuk menemukan setiap proses yang tidak memberikan nilai tambah dan menghilangkannya. Dalam hal ini, perusahaan harus melakukan analisis terhadap setiap proses produksi dan mengevaluasi apakah proses tersebut memberikan nilai tambah atau tidak.
3. Flow (Aliran)
Prinsip ketiga adalah memperbaiki aliran proses produksi agar lebih lancar dan mengurangi waktu tunggu antar proses. Hal ini bertujuan untuk mengurangi waktu siklus produksi dan meningkatkan efisiensi.
Dalam hal ini, perusahaan harus memastikan bahwa setiap proses produksi dilakukan secara berurutan dan tidak terdapat waktu tunggu yang tidak perlu.
4. Pull
Prinsip keempat adalah mengadopsi sistem pull, yaitu memproduksi hanya ketika ada permintaan dari pelanggan. Dalam sistem pull, proses produksi dimulai ketika ada permintaan dari pelanggan, sehingga tidak ada produk yang tidak terjual. Prinsip ini bertujuan untuk mengurangi persediaan bahan baku dan produk jadi yang tidak terjual.
5. Perfection (Kesempurnaan)
Prinsip kelima adalah mencapai kesempurnaan dalam proses produksi dengan terus melakukan perbaikan. Hal ini bertujuan untuk meningkatkan efisiensi dan mengurangi pemborosan.
Dalam hal ini, perusahaan harus terus melakukan evaluasi dan perbaikan terhadap setiap proses produksi untuk mencapai kesempurnaan.
Sejarah Lean Manufacturing
Konsep dasar lean manufacturing telah ada selama berabad-abad, tetapi baru benar-benar memiliki konsep yang jelas setelah adanya tulisan Benjamin Franklin tentang pengurangan limbah yang berjudul Poor Richard’s Almanack. Dalam tulisannya, menghindari biaya yang tidak perlu dapat memberikan lebih banyak keuntungan daripada meningkatkan penjualan.
Lalu Franklin meletakkan ide dan konsep lainnya dalam esai yang berjudul The Way to Wealth. Kemudian diperluas dalam buku karya seorang insinyur mesin, Frederick Winslow Taylor, Principles of Scientific Management yang terbit pada tahun 1911.
Namun, justru Shigeo Shingo dan Taiichi Ohno dari Toyota Motor Corporation yang benar-benar mengembangkan pandangan ini menjadi apa yang kemudian disebut sebagai lean manufacturing. Shingo sangat terkesan untuk menjadikan studi dan praktik manajemen ilmiah sebagai pekerjaan hidupnya setelah membaca Principles of Scientific Management karya Frederick Taylor.
Setelah sebelumnya menjadi perusahaan tekstil, Toyota mulai memproduksi mobil pada tahun 1934 dan memenangkan kontrak truk dengan pemerintah Jepang pada tahun 1936.
Namun, saat Kiichiro Toyoda, pendiri Toyota Motor Corporation, mengarahkan pekerjaan pengecoran mesin, dia menemukan masalah dengan pembuatannya, termasuk sumber daya yang terbuang untuk perbaikan coran berkualitas rendah.
Akhirnya, Toyoda melakukan studi terhadap setiap tahapan proses produksi dan membentuk tim perbaikan 'Kaizen' untuk mengatasi masalah tersebut. Hasil temuan tim Kaizen ini digaungkan oleh Taiichi Ohno untuk membuat Toyota Production System (TPS).
Pada periode pasca perang di akhir tahun 1940-an, tingkat permintaan ekonomi Jepang rendah, jadi Ohno menentukan bahwa jadwal kerja harus didorong oleh penjualan aktual daripada target penjualan atau produksi. Ini berarti menghindari kelebihan produksi yang mahal dan mengarahkan Toyota untuk membuat penjadwalan produksi pull (atau build-to-order) daripada penjadwalan produksi push.
Pada tahun 1950-an, TPS mulai menarik perhatian dunia dan diadopsi oleh beberapa perusahaan manufaktur di Jepang. Pada tahun 1980-an, konsep lean manufacturing mulai dikenal di Amerika Serikat dan Eropa setelah Toyota berhasil memenangkan persaingan dengan perusahaan mobil Amerika dan Eropa. Sejak itu, lean manufacturing menjadi salah satu metode produksi yang paling populer di dunia dan diadopsi oleh berbagai perusahaan di berbagai sektor.
Pada 1980-an, Toyota Production System yang dikenal sebagai manufaktur just-in-time berkembang menjadi lean manufacturing pada akhir 1980-an hingga 1990-an.
Seorang insinyur kualitas bernama John Krafcik pertama kali menciptakan istilah lean manufacturing dalam artikelnya tahun 1988 'Triumph of the Lean Production System' setelah mengerjakan usaha patungan antara Toyota dan General Motors di California.
Krafcik menyatakan bahwa industri yang menerapkan lean manufacturing memiliki tingkat produktivitas/kualitas yang lebih tinggi daripada non-lean dan tingkat teknologi pabrik tampaknya tidak banyak berpengaruh pada kinerja operasi.
Krafcik menambahkan bahwa risiko menerapkan proses lean dapat dikurangi dengan mengembangkan tenaga kerja yang terlatih dan fleksibel, desain produk yang mudah dibangun dengan kualitas tinggi, dan jaringan pemasok yang mendukung dan berkinerja tinggi.
Keuntungan dan Kekurangan Lean Manufacturing
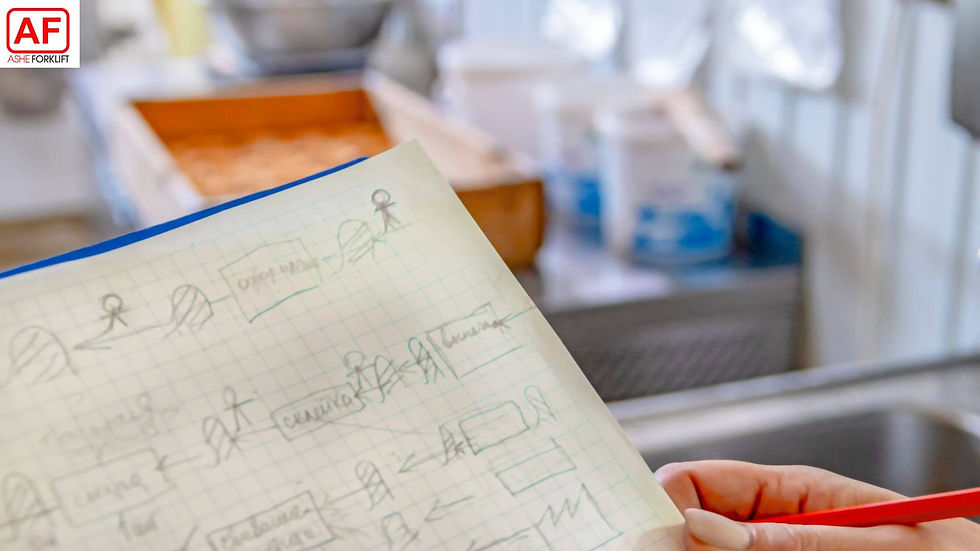
Dengan menerapkan prinsip-prinsip lean manufacturing, perusahaan dapat memperoleh beberapa keuntungan dan kekurangan, antara lain:
Keuntungan:
1. Meningkatkan efisiensi dan produktivitas
Dengan menghilangkan pemborosan dan meningkatkan efisiensi proses produksi, perusahaan dapat meningkatkan produktivitas dan menghasilkan lebih banyak produk dalam waktu yang lebih singkat.
2. Mengurangi biaya produksi
Dengan mengurangi pemborosan dan meningkatkan efisiensi proses produksi, perusahaan dapat mengurangi biaya produksi dan meningkatkan keuntungan.
3. Meningkatkan kualitas produk
Dengan memfokuskan pada kebutuhan dan keinginan pelanggan serta melakukan perbaikan terus-menerus pada proses produksi, perusahaan dapat berfokus pada peningkatan kualitas produk.
4. Meningkatkan kepuasan pelanggan
Dengan memfokuskan pada kebutuhan dan keinginan pelanggan serta meningkatkan kualitas produk, perusahaan dapat meningkatkan kepuasan pelanggan dan membangun hubungan jangka panjang dengan pelanggan.
5. Mengurangi waktu tunggu antar proses
Dengan memperbaiki aliran proses produksi, perusahaan dapat mengurangi waktu tunggu antar proses dan meningkatkan efisiensi.
6. Ramah lingkungan
Mengurangi pemborosan waktu dan sumber daya serta menghapus proses yang tidak perlu dapat menghemat biaya penggunaan energi dan bahan bakar. Ini memiliki manfaat lingkungan yang jelas, seperti halnya penggunaan peralatan yang lebih hemat energi, yang juga dapat menawarkan penghematan biaya.
7. Mengurangi persediaan bahan baku dan produk jadi
Dengan mengadopsi sistem pull, perusahaan dapat mengurangi persediaan bahan baku dan produk jadi yang tidak terjual.
Kekurangan:
1. Keselamatan dan Kesejahteraan Karyawan
Terdapat kritik terhadap metode produksi ini, dimana terdapat kemungkinan mengabaikan keselamatan dan kesejahteraan karyawan. Dengan berfokus pada menghilangkan pemborosan dan merampingkan prosedur, tekanan yang ditempatkan pada karyawan dapat diabaikan.
Lean manufacturing telah dibandingkan dengan teknik manajemen ilmiah abad ke-19 yang diperangi oleh reformasi tenaga kerja dan diyakini sudah usang pada tahun 1930-an.
2. Menghambat Pembangunan Masa Depan
Fokus yang melekat pada pemotongan pemborosan dapat mengarahkan manajemen untuk memotong area perusahaan yang tidak dianggap penting untuk strategi saat ini. Padahal, ini mungkin penting untuk warisan perusahaan dan pengembangan masa depan. Metode ini dapat menciptakan fokus berlebihan pada saat ini dan mengabaikan masa depan.
3. Sulit untuk Distandarkan
Beberapa kritik menunjukkan bahwa lean manufacturing merupakan budaya daripada metode yang ditetapkan, yang berarti bahwa tidak mungkin untuk membuat model standar. Hal ini dapat menciptakan persepsi bahwa metode ini adalah teknik yang longgar dan tidak jelas daripada teknik yang kuat.
Tips dalam Menerapkan Proses Lean Manufacturing
Terdapat empat langkah yang dapat Anda ambil untuk membantu menciptakan sistem manajemen proyek lean manufacturing Anda sendiri:
1. Merancang Sistem Manufaktur Sederhana
Semakin Anda memecah sistem Anda menjadi bagian-bagian komposit yang sederhana, semakin mudah masing-masing untuk memantau kinerja bisnis.
2. Terus Mencari Cara untuk Meningkatkan
Tim di semua bagian dan tingkatan harus didorong dan didukung dalam mencari cara untuk meningkatkan proses dan prosedur. Penting untuk memiliki tinjauan prosedur yang jujur untuk menemukan area untuk perbaikan. Semakin spesifik peningkatan ini untuk perusahaan dan proses khusus Anda, semakin efektif jadinya.
3. Terus Menerapkan Peningkatan Desain
Mencari perbaikan saja tidak cukup. Ini perlu diimplementasikan melalui desain, prosedur, dan proses Anda. Tidak cukup hanya mencari perbaikan, mereka juga perlu ditingkatkan hingga pada tahap praktis. Setiap peningkatan juga harus didukung oleh metrik peningkatan.
4. Carilah Dukungan Staf
Untuk mencapai tiga langkah di atas secara efektif, Anda perlu mendapatkan dukungan dari seluruh staf Anda. Seluruh metodologi bisa kacau jika manajemen memutuskan untuk menerapkannya tanpa mendapatkan dukungan dari karyawan.
Kesuksesan lean manufacturing tidak dapat dicapai apabila tidak memiliki tenaga kerja yang loyal dan berkualitas. Solusi untuk ini adalah membuat 'rencana ramping' di mana seluruh tim dapat memberikan umpan balik dan saran kepada manajemen, yang kemudian membuat keputusan akhir tentang setiap perubahan. Coaching juga penting untuk menjelaskan konsep dan memberikan pengetahuan kepada karyawan di semua tingkatan.
Ashe Forklift Sebagai Pendukung Lean Manufacturing Anda
Itulah salah satu jenis metode industri yang perlu Anda ketahui sebelum dapat menerapkannya sesuai dengan kebutuhan Anda. Bagi Anda yang membutuhkan alat berat tetapi tidak mau pusing memikirkan biaya perawatan dan hal-hal lainnya, asheforklift.com merupakan solusi dari permasalahan Anda.
Kami merupakan perusahaan penyewaan berbagai jenis forklift yang dapat Anda pilih. Tidak perlu lagi untuk memikirkan biaya perawatan dan biaya penyimpanan, Anda cukup menggunakan deretan jenis forklift yang tentunya berkualitas dari kami.
Comments